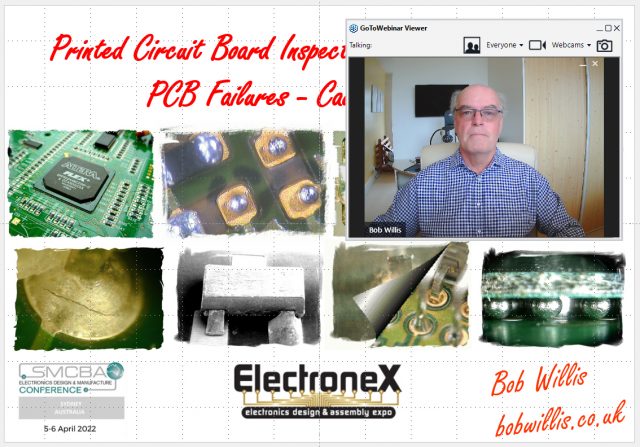
It was a please to present two workshops online for the SMCBA Sydney, Australia this week. Great questions and a good attendance at both sessions
The workshop outlines are shown below:
Printed Circuit Board Inspection & Field Failures – Causes and Cures
Workshop Introduction:
The printed circuit board is the building block of any electronic assembly and as such must exceed specification and be totally compatible with the assembly processes used in modern assembly. Failures in PCBs can be cosmetic, often the most common reason for rejection in manufacture or assembly. Failures can be found during assembly and final test which are not ideal but much better than field returns.
In his presentation Bob Willis will highlight test methods you can try and tricks of the trade to understand how PCBs can fail and how to eliminate many of the common causes. During breaks and at the end of the presentation there is a Q&A session which provides ample time for all delegate questions to be answered. However, if a delegate has a process example and photograph they would like covered in the session it will need to be provided in advance
Selected topics covered
Company PCB specification requirements
International standards
Through hole plating failures
CAF contamination shorts
PCB Delamination
Nickel/Gold – Black pad & Black Tar
Inner layer separation
Solder mask cracking
Outgassing
Need for product specifications
Auditing a PCB supplier
Who should attend?
All of the instructors workshops are designed for staff involved in design, soldering and inspection, process engineers, supervisors and production operators potentially involved with the introduction of new technology Plus those engineers tasked with quality improvement projects or staff involved in training will also benefit the early insight to future technology
Counterfeit Component Avoidance, Inspection & Failures – Causes & Cures
Workshop Introduction:
Quality, purchasing, design and production engineers need to review the growing commercial and technical issues surrounding counterfeit electronic components. This problem has been seen again due to shortages caused by the worldwide pandemic. They can look right, solder to the PCB but just fail to function. A typical first assumption by test engineering, it’s a component failed due to the assembly process, but its what’s inside the package that counts, sometimes its nothing at all.
Rather than making complicated copies of parts the simplest thing is to remark the packaging or the component body. Remarking the packaging is simple and quick, provided the component identification is not checked all the parts would be placed and soldered to the board before the problem was identified. AOI should find incorrectly marked or variations on the parts but the level of sophistication in marking is now becoming very sophisticated.
The workshop will not only illustrate the problems raised by counterfeit components within the electronics industry but it will also show you some of the different test methods that can be used to confirm the integrity of the components. Failure analysis techniques are now frequently being used to see if components are what they say they are rather than finding failure modes. Hands on workshops in the UK show that counterfeiting is still a reality, we can find them, there is no hiding place! The session also includes a FREE set 28 training wall charts covering testing and counterfeit avoidance procedures for each registered delegate to use on site
Who should attend?
This workshop is designed for design, process and quality engineers responsible for introducing procedures and testing to avoid the counterfeit components being integrated to products.. Much of the material presented is extremely visual and practical making it ideal for manufacturing staff, like all the instructors workshops it not just theory, it’s a “How to Do It Session”
Workshop Topics Included:
Component trends in industry
Counterfeit Avoidance strategy
Component Identification Checksheet
Component obsolescence
Impact of lead-free on component availability
Typical examples of component counterfeits
Guidelines on reducing the possibility of counterfeits
The different types of counterfeit
Mechanical testing component packaging
Destructive and non-destructive
Electrical testing of components
Visual & microscopic inspection
Solvent testing
XRF techniques
X-ray inspection of passive and active parts
Practical examples of counterfeit components found
Using Free On Line Defect Database